El 20 de mayo, Tan Thang Cement Joint Stock Company celebró la ceremonia de inauguración del sistema de generación de calor residual (WHR) con una capacidad de 8650 kW. Este avance tecnológico permitirá reducir las emisiones de CO2, ahorrar energía y contribuir al objetivo de desarrollar una industria cementera sostenible en Vietnam.
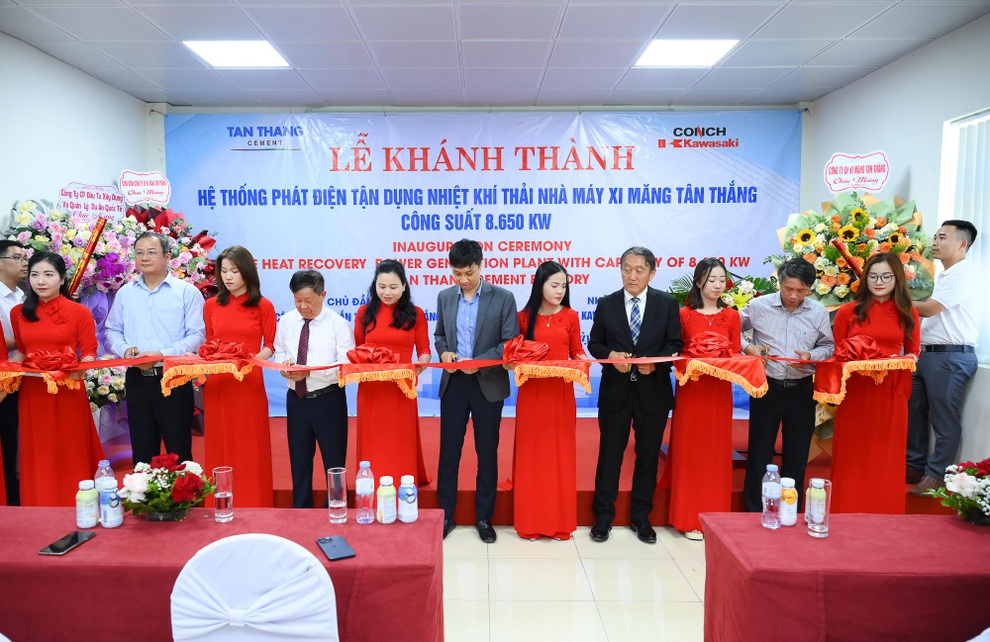
En consecuencia, el sistema WHR ha sido operado comercialmente por esta empresa en la fábrica de cemento Tan Thang (comuna de Tan Thang, distrito de Quynh Luu, Nghe An ) desde el 30 de abril. Después de un período de operación y mantenimiento, hoy el sistema ha sido aceptado por la empresa y puesto en la cadena de producción de la fábrica.
El Sr. Hoang Anh Tuan, Director General de Tan Thang Cement Joint Stock Company, afirmó: «El sistema tiene una capacidad diseñada de 9000 kW para la línea de producción de clínker de 5000 toneladas diarias. Con una capacidad bruta de 8650 kW y una capacidad neta de 8035 kW, permite ahorrar aproximadamente un tercio del consumo energético de toda la fábrica. Esto no solo representa un avance tecnológico significativo, sino que también genera importantes beneficios económicos con un periodo de amortización de tan solo unos seis años».
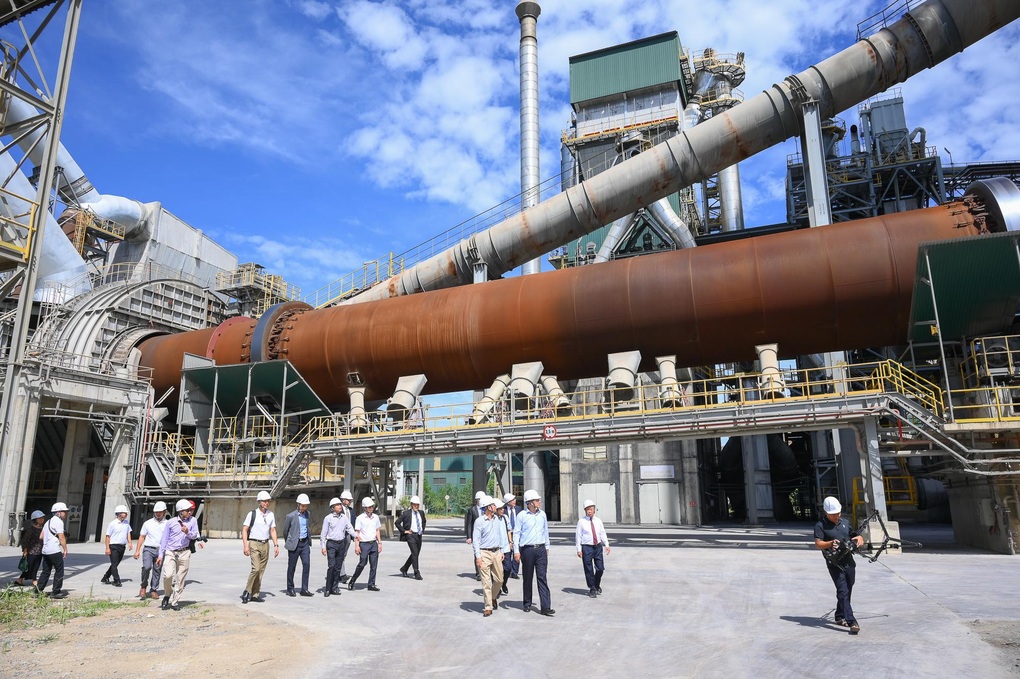
El sistema de recuperación de calor del proceso de residuos en la fábrica de cemento Tan Thang ha generado electricidad para abastecer la producción.
El sistema aprovecha el calor residual del escape en la parrilla de enfriamiento del clínker y la torre de intercambio de calor (ciclón). Esta es una fuente de calor de alta temperatura (aproximadamente 250-400 °C) y gran caudal. Posteriormente, los gases de escape calientes se conducen a través del intercambiador de calor hasta el sistema de caldera a presión mediante la turbina, generando electricidad.
El sistema WHR aprovecha al máximo el calor del 100 % de los gases residuales generados durante el proceso de producción para generar electricidad, lo que reduce las emisiones en aproximadamente 40 000 toneladas de CO2 al año. La concentración de polvo emitido al medio ambiente se reduce drásticamente de 30 mg/Nm³ a tan solo 10 mg/Nm³, de acuerdo con las estrictas normas medioambientales de la UE y el G7.
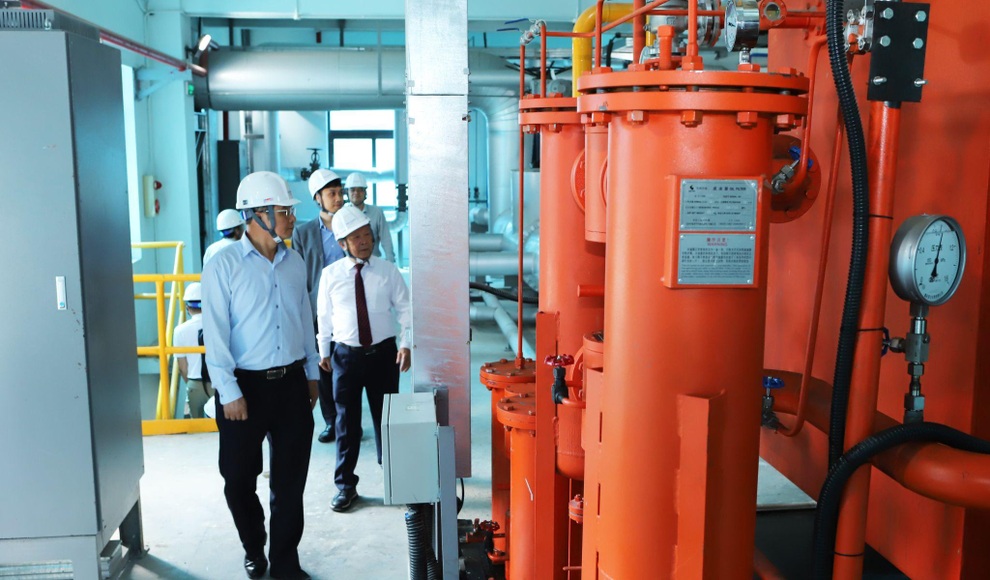
Al utilizar el calor residual para generar electricidad, la fábrica de cemento Tan Thang ahorrará alrededor de 80 mil millones de VND en facturas de electricidad cada año.
El sistema aporta beneficios duales en eficiencia energética, ahorrando entre 25 y 30% de la cantidad de electricidad comprada a EVN, ayudando a la fábrica a reducir entre 78 y 80 mil millones de VND por año, al tiempo que contribuye significativamente a la seguridad energética y reduce la presión sobre el sistema nacional de transmisión de energía, especialmente durante la temporada alta.
La puesta en funcionamiento comercial del sistema es un hito importante en el proceso de consecución del objetivo de ahorro energético, protección del medio ambiente, mejora de la eficiencia de los recursos y desarrollo sostenible de Tan Thang Cement. Esto también constituye una base fundamental para que Tan Thang cumpla con los requisitos para solicitar la etiqueta de "cemento verde" y avanzar hacia la producción en masa de líneas de productos respetuosos con el medio ambiente, afirmó el representante de la empresa.
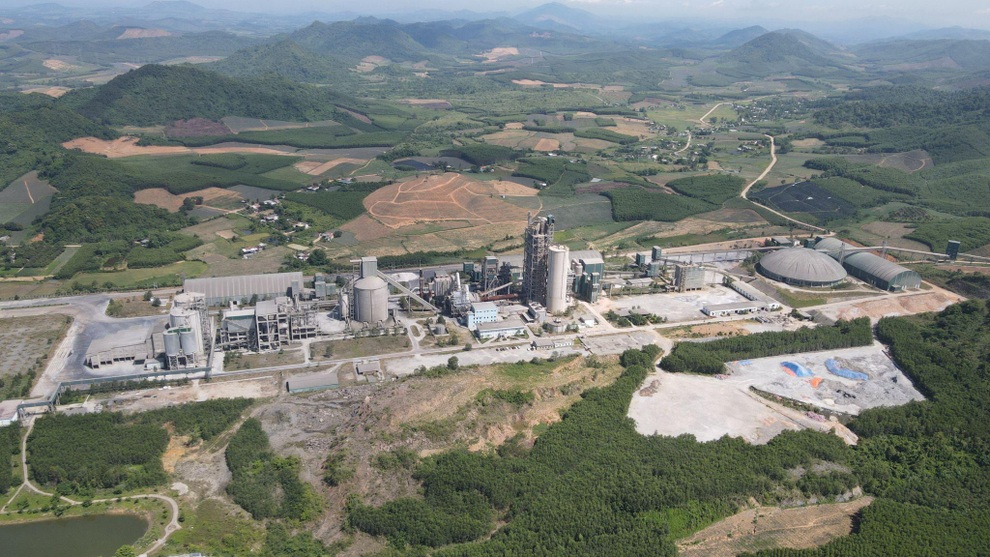
La fábrica de cemento Tan Thang tiene una capacidad de 5.000 toneladas de clínker/día, equivalente a aproximadamente 1,96-2 millones de toneladas de cemento/año.
El representante del contratista, Shanghai Conch Kawasaki Engineering Co., Ltd., afirmó que, con una larga trayectoria en la fabricación de líneas de equipos para fábricas de cemento, esta unidad ha suministrado hasta la fecha más de 300 líneas y equipos modernos de todo tipo. En Vietnam, la unidad se comercializó por primera vez en 2002. En cuanto al sistema de generación de energía térmica a partir de gases residuales, la empresa lo suministró por primera vez en Vietnam en 2014 a la fábrica de cemento Chinfon Hai Phong , y el sistema sigue funcionando correctamente a día de hoy.
En el Proyecto WHR de la Planta de Cemento de Tan Thang, además de las líneas de equipos estándar, la contratista Shanghai Conch Kawasaki Engineering también introdujo por primera vez un nuevo sistema de caldera de vapor de alta presión, que ofrece una mayor eficiencia de generación de energía que los productos existentes en el mercado. Durante el proceso de implementación, el plazo de construcción se redujo de 15 a 9,5 meses.
Al evaluar el sistema de generación de energía térmica con gases residuales, el Sr. Nguyen Quang Cung, presidente de la Asociación de Cemento de Vietnam, enfatizó: «El sistema de generación de energía térmica con gases residuales de la fábrica de cemento Tan Thang es un sistema exitoso y sistemático. Esto es el resultado de una buena planificación de la planta, la selección de consultores y contratistas, y la gestión del proyecto. La implementación de este sistema no solo ayuda a las empresas a reducir sus costos de consumo eléctrico, sino que también contribuye significativamente a la protección del medio ambiente y al desarrollo sostenible».
El proyecto no solo contribuye a la implementación de la Estrategia Nacional de Crecimiento Verde del Gobierno para el período 2021-2030, con visión a 2050, sino que también demuestra la responsabilidad de las empresas con el compromiso de reducir las emisiones netas a cero para 2050, asumido por Vietnam en la COP26. Se espera que la tecnología de recuperación de calor para la generación de energía cree un modelo de producción típico que pueda replicarse en la industria del cemento, una de las industrias con mayor consumo de energía y mayor emisión de gases de Vietnam.
Fuente: https://dantri.com.vn/kinh-doanh/xi-mang-tan-thang-tiet-kiem-80-ty-dongnam-nho-phat-dien-tu-nhiet-khi-thai-20250521115928367.htm
Kommentar (0)