On May 20, Tan Thang Cement Joint Stock Company held the inauguration ceremony of the waste heat generation system (WHR) with a capacity of 8,650 kW. This is a technological breakthrough to reduce CO2 emissions, save energy and contribute to the goal of developing a sustainable cement industry in Vietnam.
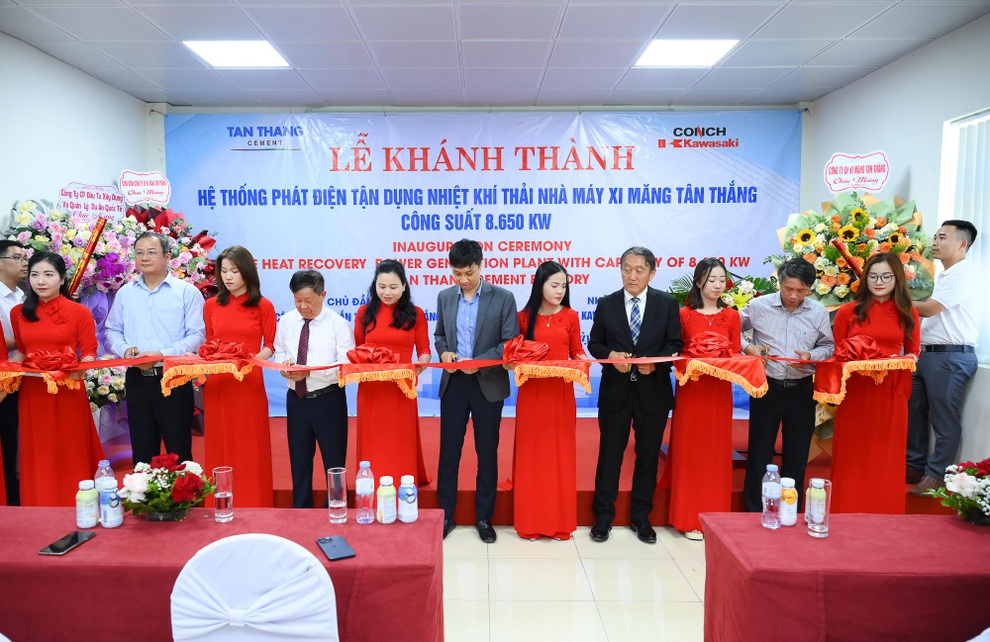
Accordingly, the WHR system has been commercially operated by this company at Tan Thang Cement Factory (Tan Thang Commune, Quynh Luu District, Nghe An ) since April 30. After a period of operation and maintenance, today the system has been accepted by the company and put into the factory's production chain.
Mr. Hoang Anh Tuan, General Director of Tan Thang Cement Joint Stock Company said: "The system has a designed capacity of 9,000 kW for the Clinker production line of 5,000 tons/day. With a Gross output capacity of 8,650 kW and a NET output capacity of 8,035 kW, it helps save about 1/3 of the power consumption for the entire factory. This is not only a significant step forward in technology but also brings high economic benefits with a payback period of only about 6 years".
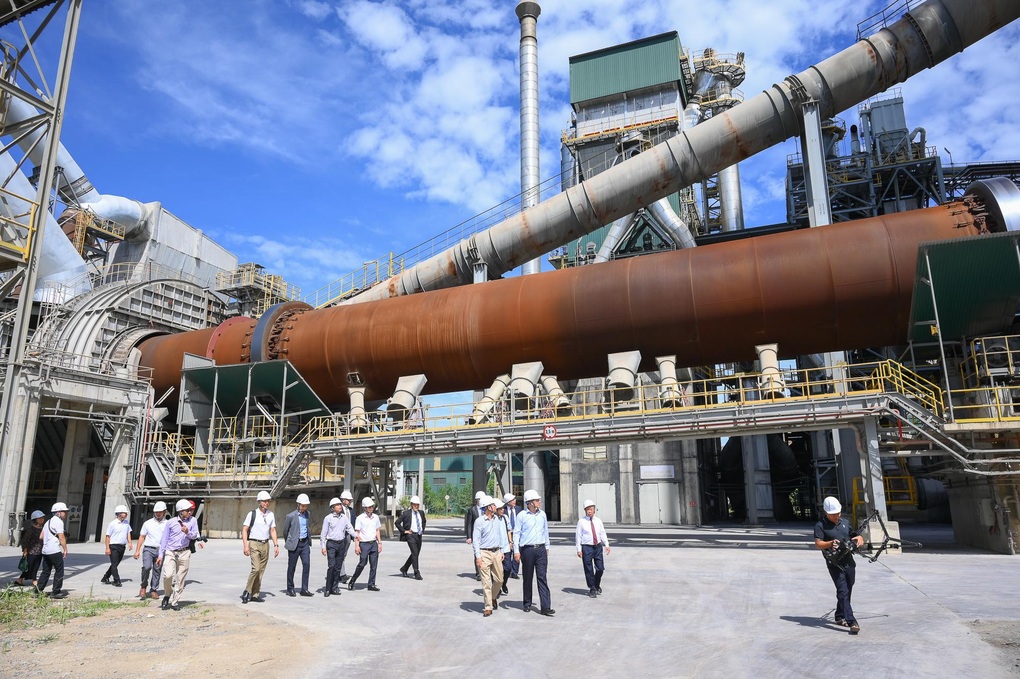
The heat recovery system from the waste process at Tan Thang Cement Factory has generated electricity to re-serve production.
The system utilizes the residual heat from the exhaust heat at the Clinker cooling grate and the heat exchange tower (cyclone). This is a heat source with high temperature (about 250-400⁰C) and large flow. Then, the hot exhaust gas is led through the heat exchanger, to the pressure boiler system through the turbine and then generates electricity.
The WHR system helps to fully utilize the heat from 100% of the waste gas generated during the production process to generate electricity, reducing emissions by about 40,000 tons of CO2/year. The concentration of dust emitted into the environment is sharply reduced from 30 mg/Nm³ to only 10 mg/Nm3 - in line with strict environmental standards of the EU and G7.
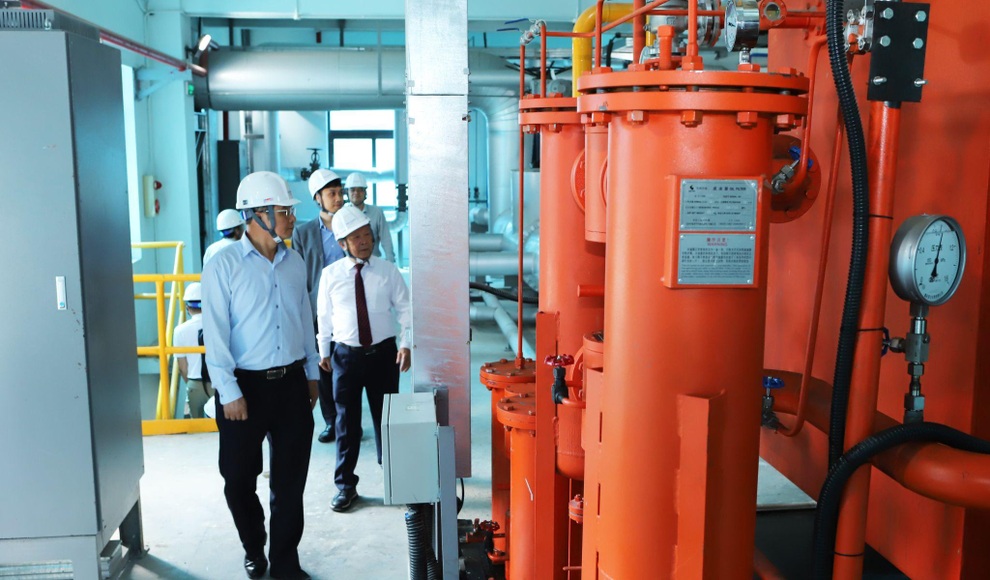
By using waste heat to generate electricity, Tan Thang Cement Factory will save about 80 billion VND in electricity bills each year.
The system brings dual benefits in energy efficiency, saving 25-30% of the amount of electricity purchased from EVN, helping the factory reduce 78-80 billion VND per year, while contributing significantly to energy security and reducing pressure on the national power transmission system, especially during peak season.
"Putting the system into commercial operation is an important milestone in the process of realizing the goal of saving energy, protecting the environment, improving resource efficiency and sustainable development of Tan Thang Cement. This is also an important foundation for Tan Thang to meet the conditions for requesting the "green cement" label, moving towards mass production of environmentally friendly product lines," said the company representative.
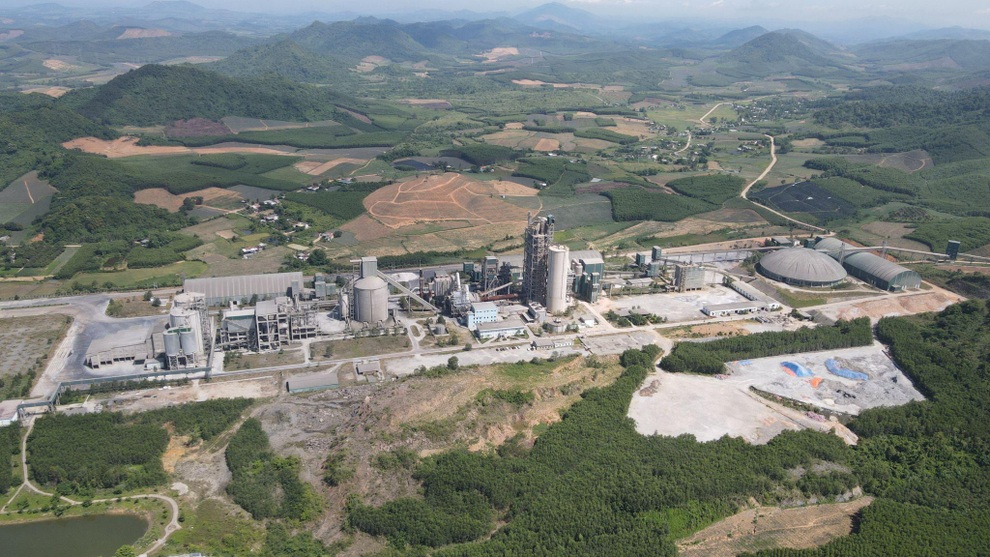
Tan Thang Cement Factory has a capacity of 5,000 tons of clinker/day, equivalent to about 1.96-2 million tons of cement/year.
The representative of the contractor, Shanghai Conch Kawasaki Engineering Co., Ltd, said that with a long history in manufacturing equipment lines for cement factories, up to now, this unit has provided more than 300 modern lines and equipment of all kinds. In Vietnam, the unit first entered the market in 2002. Regarding the waste gas heat power generation system, in 2014, the company first supplied it in Vietnam to the Chinfon Hai Phong cement factory and the system is still operating well to this day.
At the WHR Project at Tan Thang Cement Plant, in addition to the standard equipment lines, the contractor Shanghai Conch Kawasaki Engineering also introduced for the first time a new high-pressure steam boiler system, providing higher power generation efficiency than existing products on the market. During the implementation process, the construction time was shortened from 15 months to 9.5 months.
Evaluating the waste gas heat power generation system, Mr. Nguyen Quang Cung - Chairman of the Vietnam Cement Association, emphasized: "The waste gas heat power generation system of Tan Thang Cement Factory is a successful and systematic system. This is the result of good planning of the factory, selection of consultants, selection of contractors, and project management. Putting into use the waste gas heat power generation system not only helps businesses reduce electricity consumption costs but also contributes greatly to environmental protection, towards green development".
The project not only contributes to the implementation of the Government's National Strategy on Green Growth for the period 2021-2030, with a vision to 2050, but also demonstrates the responsibility of enterprises with the commitment to bring net emissions to "0" (Net Zero) by 2050 that Vietnam made at the COP26 Conference. Heat recovery technology for power generation is expected to create a typical production model that can be replicated in the cement industry, one of the largest energy consuming and emission-emitting industries in Vietnam.
Source: https://dantri.com.vn/kinh-doanh/xi-mang-tan-thang-tiet-kiem-80-ty-dongnam-nho-phat-dien-tu-nhiet-khi-thai-20250521115928367.htm
Comment (0)